Challenge
Our client, a well-established manufacturer in the blow molding industry, required a fully integrated conveyor system to optimise the flow of plastic preforms and blown bottles within their production facility. The project presented several key challenges:
- Limited space between the blow molding machine and the filler, restricting conventional accumulation options.
- Slow filler speeds, which required a solution to maximise accumulation and keep the blow molder running efficiently.
- Handling empty bottles on a spiral system, a first-of-its-kind challenge.
- Multiple product sizes, necessitating a height-adjustable conveyor solution.
The Solution
Asmech Systems Ltd engineered, manufactured, installed, and commissioned a bespoke conveyor system to meet these challenges. The solution included:
-
Preform Handling & Conveyance:
- Plastic preforms were received from a bin tipper and transferred onto a modular preform conveyor leading to the blow molding machine.
-
Blown Bottle Transport & Accumulation:
- Freshly blown bottles were transferred onto a height-adjustable slat conveyor, accommodating different product sizes.
- Due to space constraints and the slow filler speeds, Asmech implemented a spiral accumulation system which was supplied by our partners at Ambaflex, not only allowing the blow molder to continue running for a longer period of time before shutting off, but also to supplement the filler while the blow molder warmed back up. This was a groundbreaking achievement, as it marked the first successful handling of empty bottles on a spiral conveyor system.
-
Automation & Control Integration:
- A new conveyor control panel was provided to seamlessly interface all system components.
- Advanced automation solutions ensured smooth coordination between the blow molder, filler, and conveyors, optimising throughput and minimizing downtime.
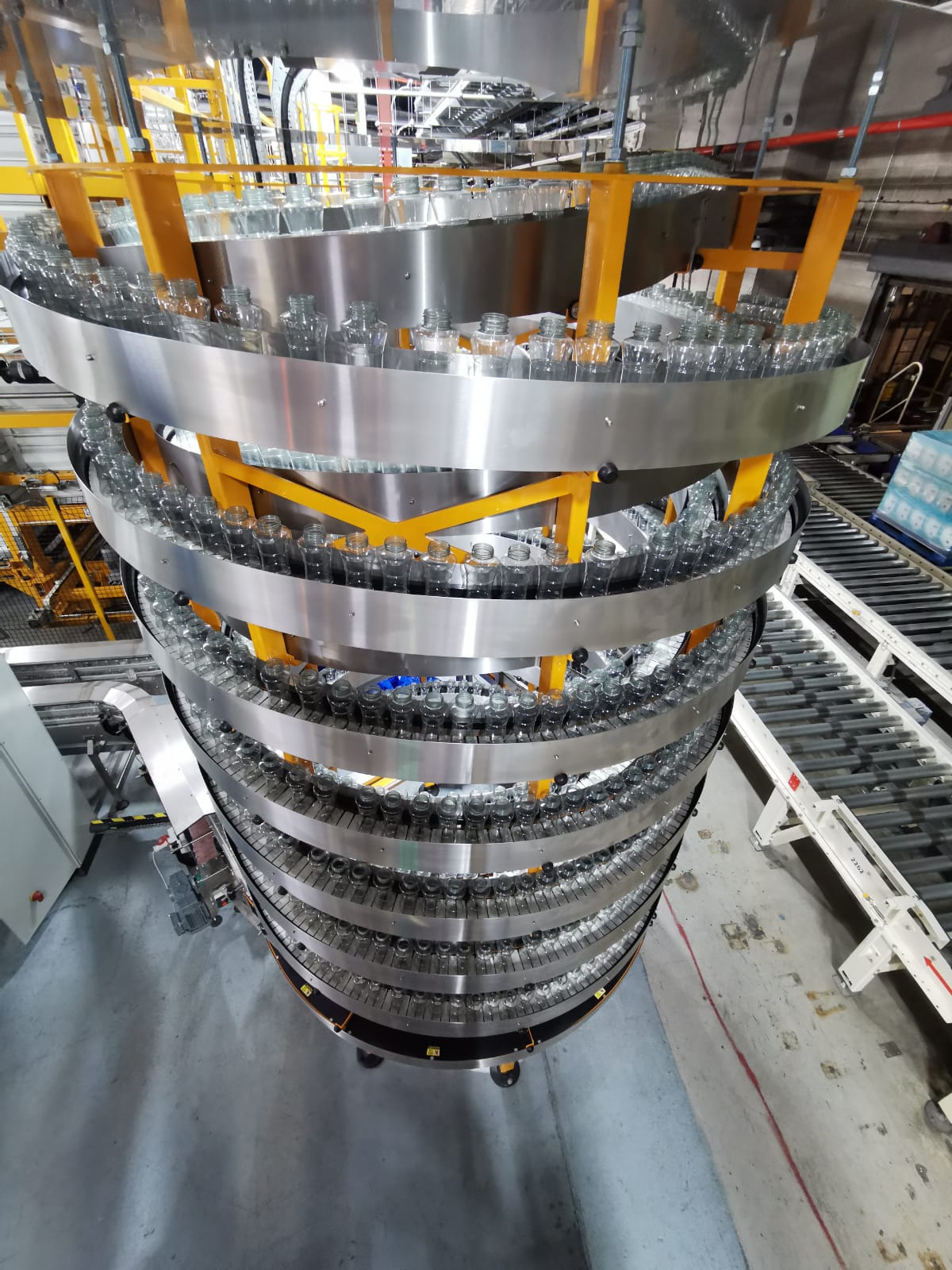
Results
- Increased production efficiency by enabling extended operation of the blow molder.
- Maximised product accumulation, ensuring a continuous supply to the filler even when the blow molder was warming up.
- Space-saving solution that overcame layout constraints.
- Successful implementation of a spiral conveyor for empty bottles, demonstrating Asmech’s engineering expertise and innovative problem-solving capabilities.
Conclusion
This project showcased Asmech Systems Ltd’s ability to design and deliver tailored conveyor solutions for complex manufacturing environments. By integrating automation, innovative conveyor technology, and space-efficient accumulation, we provided our client with a seamless and efficient production process.
Do you have a similar challenge in your production facility? Contact Asmech Systems Ltd today on 01623 424442 or email us at sales@asmechsystems.co.uk to discuss your bespoke conveyor solution.