Overview
Asmech Systems Ltd recently partnered with a major brewery to upgrade and integrate a series of conveyors and machinery into their production line. The goal was to streamline the movement of empty cans from depalletising through to end-of-line packing stations, ensuring seamless, efficient, and reliable operations.
Challenge
The client needed a system capable of:
- Accepting singulated empty cans from a depalletiser.
- Ensuring seamless transitions through multiple processes, including filling, drying, labelling, and packing.
- Removing faulty cans efficiently without disrupting the production line.
- Automating key processes to reduce manual handling and improve efficiency.
The Solution
Asmech Systems Ltd delivered a comprehensive solution that integrated multiple stages of the brewery production line:
-
Empty Can Handling
- Singulation & Transfer: Empty cans were singulated from the depalletiser and lowered onto a newly installed slat conveyor via a can twist.
- Filler Integration: The cans were conveyed directly to the filler, ensuring precise alignment and smooth operation.
-
Post-Fill Conveyor System
- Reject Unit Installation: A new slat conveyor was installed to handle cans from the filler. Faulty cans were removed by a reject unit and diverted onto a rotary table for inspection and disposal.
- Accumulation Table: Accepted cans were conveyed to an accumulation table, providing buffer capacity to optimise line efficiency.
-
Drying and Labelling
- Can Dryer: After accumulation, the cans passed through a drying station to prepare them for labelling.
- Labelling Integration: Individual cans were labelled with precision on a dedicated labeller.
-
Coding and Packing
- Ink Jet Coding: A side grip conveyor transported the cans above an ink jet coder to mark them with essential information.
- End-of-Line Packing:
- Filled and labelled cans were transferred to the packing station, where they were placed into boxes.
- Boxes were sealed using a tape sealing machine, labelled with outer packaging information, and palletised for shipping.
-
Control & Automation
-
- A new conveyor panel and advanced automation interface were provided to integrate all systems seamlessly.
- Asmech ensured smooth communication and synchronisation between various processes to minimise downtime and optimise performance.
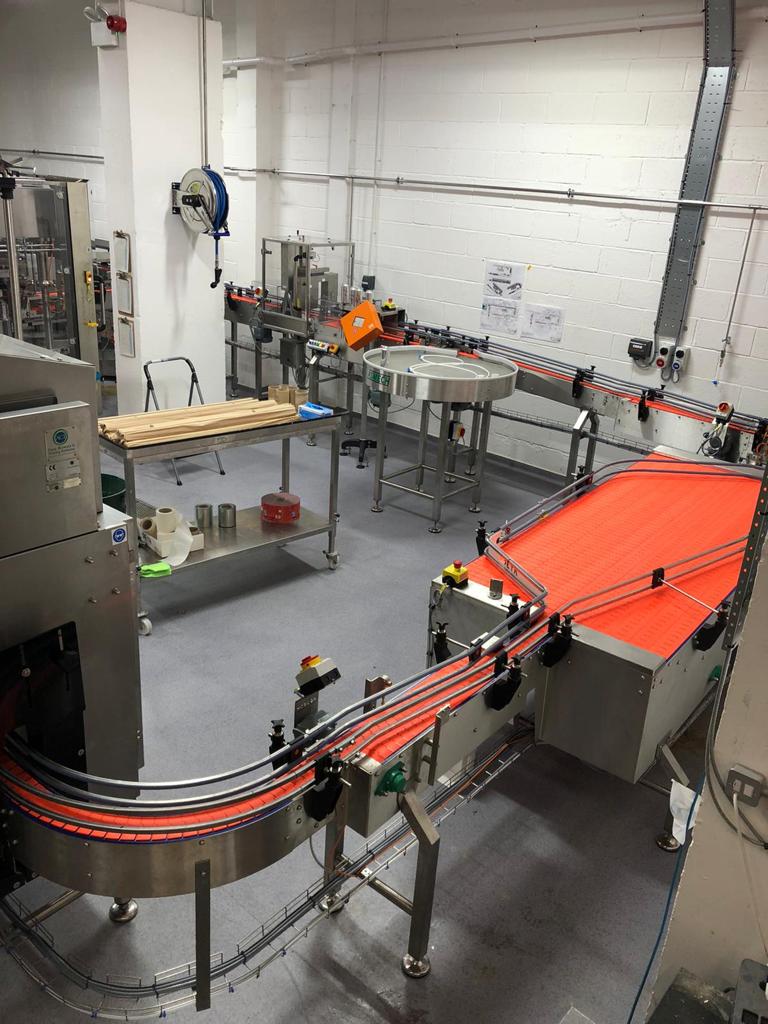
Project Execution
Asmech Systems Ltd handled multiple aspects of the project, including:
- Design: Customised solutions to fit seamlessly within the client’s existing layout.
- Manufacturing: Produced high-quality conveyors and system components at Asmech’s state-of-the-art facility.
- Installation: Expert engineers ensured quick and efficient installation to minimize downtime.
- Commissioning: Thorough testing and calibration to ensure optimal performance.
- Project Management: Oversaw all stages, maintaining clear communication with the client to deliver the project on time and within budget.
Outcome
The upgraded production line has significantly improved the brewery’s operational efficiency and quality control. The client has reported smoother transitions between processes, reduced waste, and an increase in overall throughput.
Why Asmech Systems Ltd?
- Over three decades of expertise in bespoke conveyor systems.
- Comprehensive project management from design to commissioning.
- Commitment to delivering tailored solutions that meet specific client requirements.
Contact Us
If you’re looking to optimise your production line, contact Asmech Systems Ltd today on 01623 424442 or email us at sales@asmechsystems.co.uk. Let us help you achieve efficiency and excellence in your operations.